As technology evolves and develops, companies are turning to creating natural fiber composites with tension control as an eco-friendly, cost-effective way to manufacture products. From cars to construction materials, these materials offer a variety of advantages for industrial utilization, but understanding how they work can take time and effort. Let’s take a look at why natural fiber composites are so powerful and how tension control can help you get the most out of them.
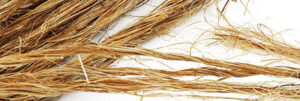
Hemp fiber
What Are Natural Fiber Composites?
Natural fiber composites are composite materials created from natural fibers such as flax, hemp, jute, and kenaf combined with thermoplastic polymers such as polypropylene or polyethylene. These materials are developed to provide strength and resilience in various industrial applications while still being eco-friendly, sustainable, and cost-effective. The materials can be used in a variety of applications. One of the most popular uses for natural fiber composites is in automotive manufacturing. These materials can be used for interior components like seat covers and dashboards, as well as exterior components like bumpers and spoilers.
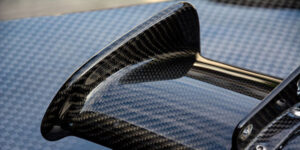
Carbon fiber composite product for motor sport
The Benefits of Using Natural Fiber Composites.
There are many benefits to using natural fiber composites in your production process. These include improved environmental sustainability, reduced costs due to their lightweight nature, better energy absorption compared to traditional materials, and improved mechanical properties that make them incredibly durable and resistant to weathering. Additionally, because they’re biodegradable, they can be recycled easily, which helps reduce waste in landfills.
Tension Control Needed To Create Natural Fiber Composites.
Creating these composites involves controlling the tension during the weaving process. Maintaining an even tension throughout the process is crucial to get a consistent product with no weak spots or bulges. Creation is done by using mechanical weaving machines equipped with tension sensors and controllers, which automatically adjust the tension according to preset parameters. The patented Vanguard System is Montalvo’s flagship closed-loop, tow, and tape tension control technology system, leading the way in precise, uniform, consistent, automated tension control.
The MVS controls even the slightest changes to ensure tension is automatically and continuously precisely where you set it. This is done through the system’s single interface for automated control, indication, and data collection of every end/tow in your process. Montalvo’s Vanguard Tension Controller (V-TC) is easy to set up and operate, utilizing the continuous feedback from the load cells. The Vanguard Load Cells (V-LC) feature Montalvo’s industry-leading load cell technology for sensitivity, reliability, and repeatability, providing exact, continuous tension measurement of your ends for higher-quality tension control. The Creel Pneumatic Brake systems smooth, consistent, precise torque control for maximum process capability. Montalvo’s Vanguard Torque Control constantly adjusts the web/ tow tension maintaining the desired tension required for the material while it is being processed.
Vanguard Individual Position Tension Control System
Conclusion:
Natural fiber composites offer an excellent option for those looking for a lightweight and cost-effective solution for industrial utilization. While these materials have many benefits, it is essential to understand the importance of maintaining an even tension throughout the production process to get optimal results from your investment in this versatile material. With proper control over tension levels during production with the Vanguard System and customization options available after production, natural fiber composites can provide long-lasting beneficial outcomes for any application needed! For more information on a system for you – https://www.montalvo.com/vanguard/