Center winding film or other extensible material comes with inherent difficulties. If you maintain a constant tension on the web, as the diameter of the roll increases, the wraps become tighter. This sometimes stretches the web. If the web just came from a dryer section and the film is warm when it is wound, it will tend to stretch more. Then as it cools, it shrinks to its original size and either telescopes the roll or crushes the core. Similar problems arise when winding extensible foam materials as well.
What is Taper Tension?
Taper tension is the process of gradually decreasing web tension as the material is wound at the re-coiler so that the larger the diameter of the coil, the lower the tension.
How to Use Taper Tension for Rewind Control
The best method of achieving taper tension is to measure the diameter of the roll, either using an ultrasonic sensor or two pulse tachometers (one on measuring revolutions of the rewind roll and one measuring revolutions of a drive roll). This measured diameter is then processed and is used to reduce the tension as the roll diameter increases. Taper Tension can be automatically controlled through a taper tension feature controller.
Montalvo has multiple controllers that can accomplish this. The Z4, the X3400HD and the S4 Digital Tension Controller. Either of these units can also calculate the roll diameter without using any external sensors. While using external sensors ensures an accurate diameter calculation (better than 1%), the internal diameter calculation is more in the 5% accuracy range. This is usually more than adequate.
Calculating Taper Tension Ratios
Montalvo controllers provide a taper tension feature for varying the rewind tension inversely with roll diameter. The degree of taper is controlled by the taper percentage entered into the controller. When the diameter of the roll doubles, the tension drops by half the taper percentage of the initial tension, where the taper percentage is the value entered into the controller. When the diameter of the rewind roll doubles again, the tension will drop by and additional quarter of the taper percentage of the original tension. When the rewind roll diameter doubles again, the tension will drop by and additional eighth. For example, when the initial tension is 80-lbs and the taper percentage is set to 40%, the tension will change from 80-lbs less 20%, (i.e. 64-lbs) when the diameter of the rewind roll doubles.
As far as the amount of taper necessary, this is mainly a trial and error operation. So much depends on the type and condition of the material, whether a lay on roll is used, etc.
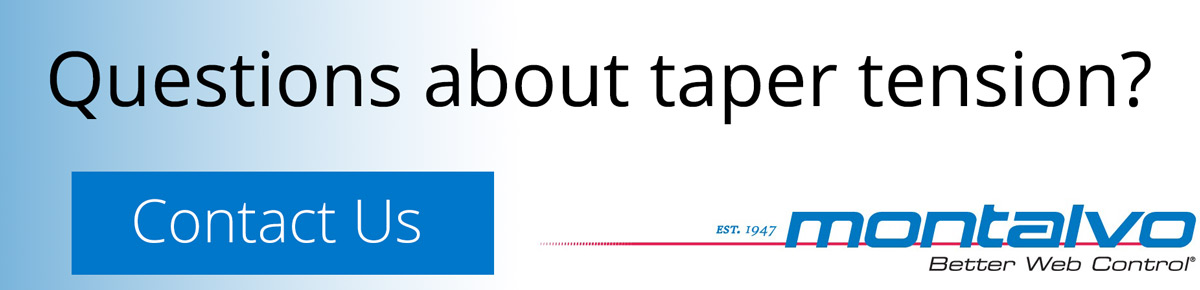
© Montalvo – Permission granted to use this copyrighted material, in part or all, provided that the source is acknowledged as © www.montalvo.com