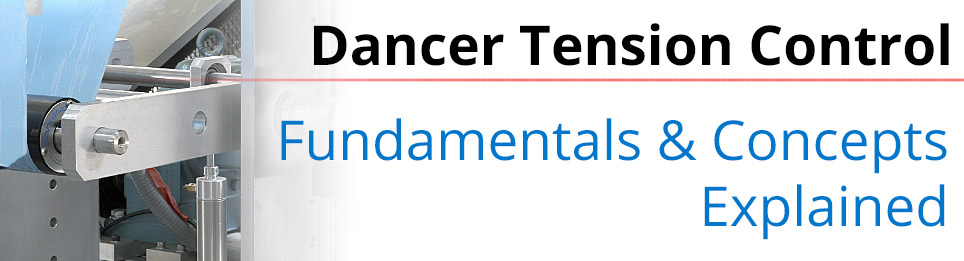
Dancer tension control systems play an integral role in the process of maintaining consistent tension while transporting a web. To ensure product quality, dancers help to stabilize and optimize tension during processing of web material. An accurately designed dancer system will meet the challenges and any issues inherent in a process to assure proper control. Poor wound roll quality as a result of telescoping, starring, or out of round webs and other roll defects can be avoided by a properly designed system.
Dancer System Components
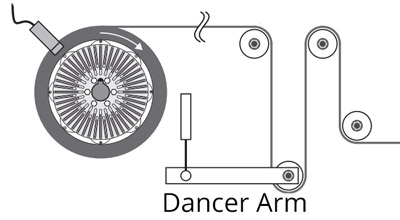
Webs cannot be controlled without proper tension and dancer systems are instrumental in providing control as material moves through an unwind or rewind process. A dancer roll system is essentially a preloaded idler arm. Its force and positioning is derived from web tension during web unwind or rewind processes, thus their design is critical to high quality functionality of a web handling process.
Tension Zones
Every system has a number of tension zones that need to be controlled to ensure quality and productivity. Tension zones are just that – areas between two places within a web that can modify or affect tension. Each tension zone is unique and must have an independent feedback loop to maintain correct tension levels. In general, there are three tension zones that need to be controlled – the unwind tension zone, the intermediate tension zone, and the rewind tension zone. For example, the unwind tension zone is between the unwind drive and the master drive; between the master drive and the slave drive web processing occurs in the intermediate tension zone.
Closed Loop Systems
Within each zone there are two control options for regulating tension, open loop or closed loop control. Dancers are utilized in closed loop tension control systems. Though there are different designs, such as pivot arm, linear and rotational, all dancer tension controls have certain commonalities. For one, they all have idler rolls or arms that are preloaded for one direction, as the web appears to move them in the opposite direction. Secondly, as a web is drawn over a dancer roll it moves in response to any changes in its position. That movement is a result of a change in web tension.
Dancer Potentiometer
A dancer’s position is monitored by a sensor that detects and controls the drive’s movement. When tension increases or decreases in a web, the dancer roll changes position that activate the sensor, known as a dancer potentiometer. The sensor signals the system to either increase or decrease the torque, i.e., speed, for the dancer to return to its original position. In that sense, dancers act more as position controllers and less as tension controllers. By maintaining control of a web’s speed, dancers keep tension constant.
Benefits of Dancer Control Systems
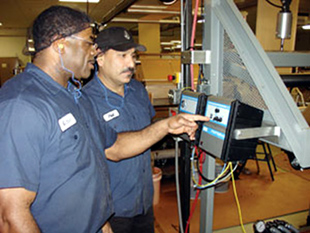
One big advantage to using dancer tension controls is that they provide a particular amount of web storage, meaning that the dancers accumulate a certain length of web in the machine direction. Its web accumulation ability allows for absorbing fluctuations in tension due to various factors like out-of-round rolls. Thus, by absorbing fluctuations in tension zones, web tension downstream of the dancer is maintained and kept smooth. Accumulation also allows for a degree of mechanical stability for large roll build ratios during unwind and rewind processes.
A web of material can vary from extremely thin foils and plastics to a variety of textiles, papers, metals, and composites. As defined, a web is a continuous roll of flexible, thin roll or strip of material. The ultimate goal is to supply the web with material at a constant tension as it winds or unwinds. Dancer tension control is essential to handling web tension and positioning of material as it is transported through the web machinery for processing. Without correct tension being applied, a web cannot be controlled.
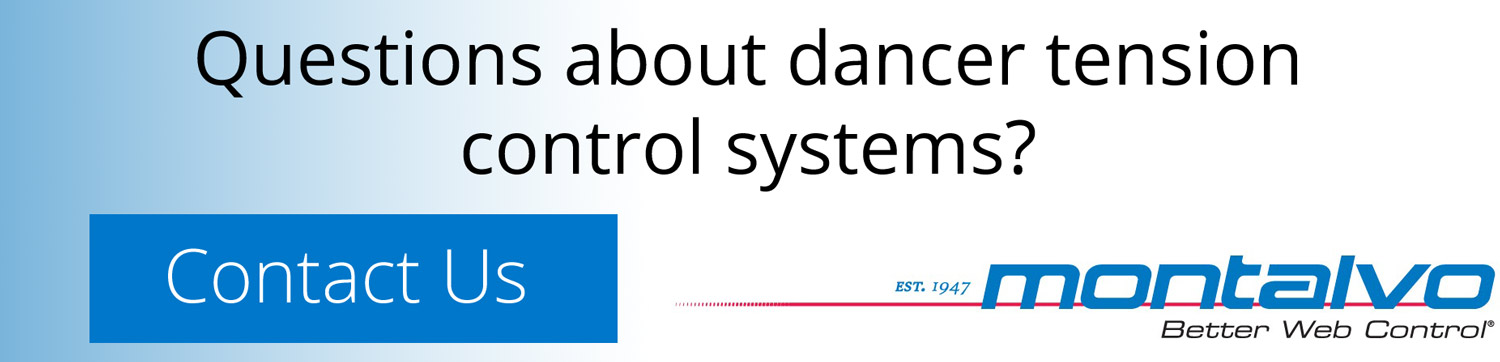