Web Breaks are the bane of converting, printing, coating, and all applications. You rarely know in advance when a web break is going to happen, and when it does the operator is often at a loss to explain why it happened. Although a complete tension control system can greatly reduce the chances of a web break occurring, when a web break does occur it is the speed at which it is detected and action taken that determines the amount of time and product loss.
What Causes Web Breaks?
Although there are some general conditions that make web breaks more likely to happen, the specific circumstances that cause web breaks vary from application to application, from press to press, and from converting machine to converting machine.
Web breaks can, for example, occur during splicing, or can occur when running a thin gauge material on a machine with a control system that is unable to maintain the necessary low tensions. When splicing for instance, runnability can be affected by the length of the splice tab, which if too long, can result in web breaks. Equally it’s important to remember that consistent roll structure in the form of in-wound tension in the roll, from the core to the outside diameter, is crucial. Inconsistent roll structure affects printability and causes various process inconsistencies to arise that include web breaks but also wrinkles and bagginess, as well as other problems.
Immediate detection of web breaks prevents hazards, reduces time loss, minimizes disruptions, and greatly reduces waste.
Utilizing Web Break Detection Sensors
Montalvo’s Web Break Detection equipped controllers enable users to program and adjust all web break detection settings, determining the level of sensitivity in triggering a web break signal, and creating the type of web break detection indication desired (ex: alarm, light, machine shutdown, etc)
Adjusting the level of sensitivity in triggering a web break signal allows users to dictate the level of tension change and length of time of that tension change that will signal a web break. This allows adjustments to be made that best meet the needs of each individual application. The versatility in outputs as a result of a web break gives users the ability to customize how the operator and machine will be alerted and react to the web break, whether it’s an alarm for the operator or automatically shutting down the machine.
Montalvo’s Web Break Detection also creates an initial delay during the run signal so that a break is not detected while the machine is getting up to speed.
Although the risk of a web break may never fully be eliminated, the risk can certainly be minimized by having a high quality complete tension control system in place. Montalvo Web Break Detection enabled controllers are just one feature of the controller, and part of a complete tension control line of products. Montalvo controllers are frequently supplied along with other devices such as tension-sensing load cells (transducers) or Montalvo pneumatic friction brakes/clutches or drive systems as part of a closed loop regulation system.
In addition to web break detection, Montalvo control modules such as the X-3400ce tension controller, an analogue controller with digital parameter handling also incorporate features such as inertia compensation, taper tension capability, transferable memory card, sample, hold and ratio splice function and the latest in communication protocol technology, i.e. DeviceNet, Profibus and CANopen.
Web Break Detection comes equipped on the following Montalvo Controllers: X-3400 Tension Controller, Z4-UD Unwind Dancer Tension Controller, and the Z4-UI Unwind Dancer Tension Controller with Tension Indication. All controllers additionally feature a wide range of communicative, diagnostic, and performance-enhancing features.
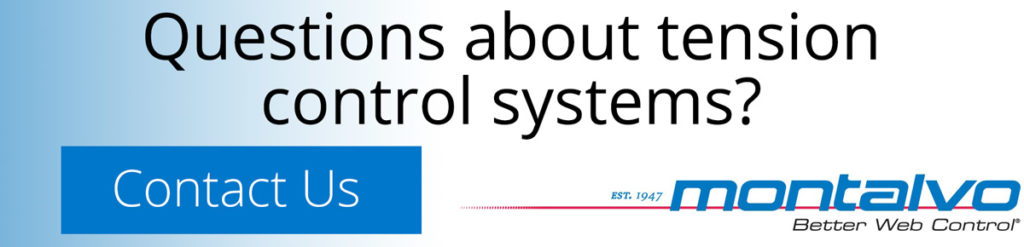
© Montalvo – Permission granted to use this copyrighted materiahttps://www.montalvo.com/contact-us/l, in part or all, provided that the source is acknowledged as © www.montalvo.com