by Henning Pedersen, Montalvo Applications Specialist henning.pedersen@montalvo.com
The trend towards faster, wider web width machinery and the processing of a broader range of substrates has resulted in a greater emphasis being placed on tension control equipment.
Without an accurate method of measurement and control, product quality and productivity will be affected. Distortions in a material, stretched as a result of excessive tension, can be just as counterproductive as folds and creases from too low a tension. Web breaks and the consequent downtime are costly affairs.
In order to control web tension, there must be continual and precise measurement of actual tension in the web in a format that is meaningful to the process line’s tension control system. That system regulates tension through drives or brakes at zones in the line that are preset to determine tension levels.
Electronic load cells are at the beginning of any sequential measurement process. They convert tension to electrical signals. The quality of that signal, as a measurement of web tension, is a key variable in determining the effectiveness of stable tension. If the signals are imprecise or fail because of poor operating conditions, the fault becomes apparent very quickly.
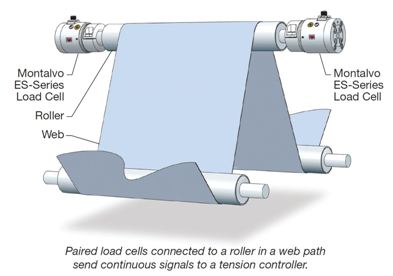
Converters are finding that production requirements are becoming more demanding and more attention is being paid to load cells as an essential in-line component. The demand for greater material flexibility and faster line speeds necessitates wide measurement ranges, signal stability and long term reliability.
Montalvo load cells (transducers) are mounted on a sensing or measuring roll in continuous contact with the web material. Depending on design and application criteria, they may be mounted beneath pillow block bearings at one or both ends of a sensing roll, or directly at the roll shaft end. System output signals are relayed to tension controllers or indicators. The load cells (transducers) are available in many different load ratings and mounting styles. Most load cells (transducers), when properly sized, provide a nominal output per pair of up to 250 mv, thereby providing a high output range. In general they offer excellent linearity and low hysteresis, even at minimum output.
Furthermore, Montalvo load cells are designed to operate over wide temperature ranges without electronic temperature compensation. In consideration of all these features, overall system resolution with a load cell (transducer) system can be as good as 1-2% of load rating.
The load cell (transducer) is the most vulnerable component of a measurement system. They are exposed to the rigors of the operating environment and consequently must be able to accommodate high speed resonance changes without experiencing signal distortions.
Failure in the quality of the signals that the load cells (transducers) produce cannot be compensated for by any other tension component. The
quality of the signals directly affects machine operating efficiency and unreliable signals result in poor quality performance, high levels of waste and excessive downtime due to the need to stop the machine and recalibrate or even replace faulty sensors.
The importance of load cells (transducers) is disproportionate to their size. Manufactured to tight tolerances, they need to be sturdy, durable and able to withstand jolts, overloads, EMC disturbances and occasional operator mishandling. In addition, they must be sensitive and exceptionally quick in determining the slightest tension fluctuation and respond accordingly. Montalvo load cells are manufactured to produce quality signals and to withstand the rigors of a manufacturing environment. These load cells use material such as stainless steel which can resist even aggressive environments. They are produced to meet IP54 and higher classifications.
Load Cell Control (Bridge) Methods
Operation of a Montalvo load cell begins with an excitation voltage applied to the load cells wired in the Wheatstone Bridge configuration. Force due to web tension deflects the load cell beams, causing compression and tensile forces on the beams. This deflection, typically only up to 0.005 inch, in turn changes strain gauge resistance values across the bridge. The end result is an output voltage directly proportional to web tension.
Excitation voltage can be supplied by a wide variety of electronic packages largely dependent upon the task at hand. For example, if a drive requires
a tension trim signal, inexpensive amplifier modules, such as a Montalvo M-3200 or Montalvo A-4 load cell amplifier module, provide excitation and calibration circuits. This type of device also provides current voltage and meter output proportional to web tension. When using load cell systems in applications requiring a PID regulator package, such as unwinds using pneumatic brakes, load cell excitation, calibration and summing circuits are included as part of the control. The initial setting up of a load cell system can usually be accomplished in a matter of minutes. A simple tare weight zeroing procedure establishes a zero point reference. This potentiometer adjustment is followed by calibration.
Load Cell System Operation “Controlling an Unwind Brake”
Again, excitation voltage is sent to a set of load cells (transducers); web tension forces create output changes that are returned to the controller. This output proportional to web tension is compared to a tension set point established by the operator. The controller electronically compares actual web tension to the desired set point and sends corrective output to the I/P Converter for brake air pressure regulation, to a voltage converter for an electric brake or to the torque input of a drive. Since the web itself is part of the feedback loop, the control can readily compensate for speed and roll diameter changes.
The same principles apply to drive applications for unwinds and rewinds. Intermediate systems differ slightly. These applications require a speed reference from a tachometer on the “master” drive to establish a speed ratio between master and slave drive motors. Together with load cell (transducer) input a corrective trim signal is sent to the slave for tension control.
Montalvo finds that the most common mounting style is a dead shaft idler. Split Pillow block and other mounting styles such as flange and single
bolt through machine mounts are also available. To accommodate slight roll misalignment, a spherical head design incorporating a bearing also compensates for shaft expansion. At the end of the head assembly is a coupling assembly used to secure the idler roll’s dead shaft. Other types of load cells consist of live shaft load cells which are also offered in several configurations, as well as under pillow block units for use with pillow block bearings and rotating head styles for use with hollow rolls without dead shafts. There are also cantilever and flat or pancake style load cells as well.
Henning Pedersen is a Montalvo Applications Specialist and Electro-Mechanical Engineer. He is responsible for sales, service and technical support for Montalvo Europe
Montalvo Europe, Jeppe Aakjaers Vej 18, DK-8700 Horsens, Denmark.
Tel: +45 75 57 27 11
Fax: +1-207-856-2509
Email: henning.pedersen@montalvo.com
Pedersen was previously the chief of electronic production for 23 years at Montalvo’s former Danarota Technic office, followed by serving as the area sales manager for Scandinavia for the former Montalvo A/S in Denmark. Pedersen holds an AF Degree in Strategy & Management and an AF Degree in Purchase & Management.
© Montalvo – Permission granted to use this copyrighted material, in part or all, provided that the source is acknowledged as © www.montalvo.com